In the ever-evolving world of manufacturing, cast iron casting stands as a testament to robust engineering and timeless reliability. This age-old technique, which has adorned our factories and infrastructures for centuries, is not just about pouring molten metal into a mold—it's about precision, expertise, and unparalleled durability. Let’s journey through the intricate world of cast iron casting to uncover why it remains a cornerstone in the realm of metallurgy and manufacturing.
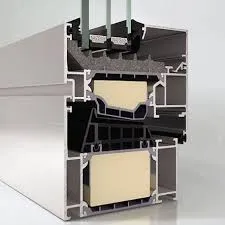
The process of cast iron casting starts with selecting the right type of iron. Gray iron, ductile iron, and malleable iron each serve different purposes, allowing industries ranging from automotive to construction to tailor products according to specific needs. The choice of material is not arbitrary; it requires a deep understanding of the product’s end-use and the stresses it will endure. This ensures that the final product is not only fit-for-purpose but exceeds expectations in terms of performance and longevity.
Cast iron’s expertise is demonstrated in its ability to produce complex geometries and intricate designs that are difficult, if not impossible, to achieve with other materials. The mold-making process is a craft in itself.
Precision and skill are paramount as the mold dictates the accuracy of the final casting. Sand casting, one of the most versatile molding methods, allows for intricate shapes and sizes, with the added benefit of cost-effectiveness. This is why industries opt for cast iron casting when they need a solution that combines durability with complexity.
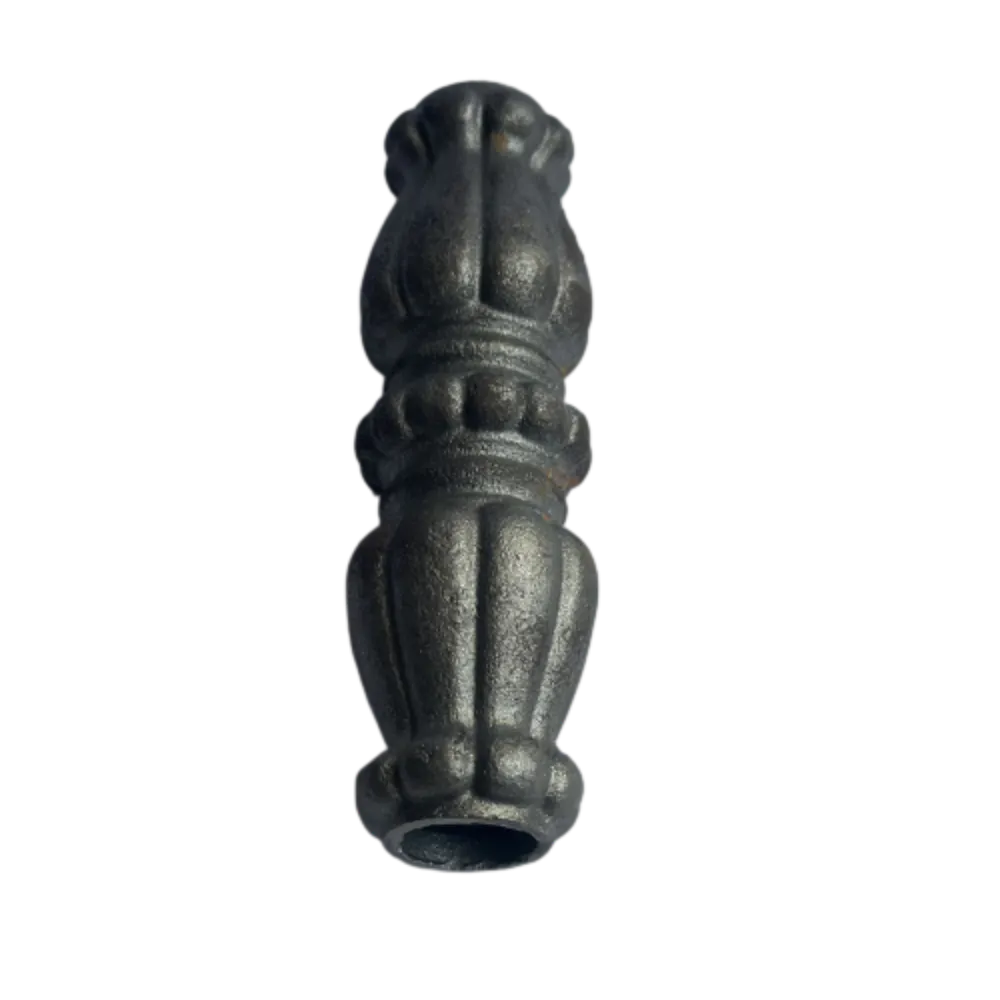
Authority in the field of cast iron casting comes from firms that have pioneered innovations and set standards of excellence over decades. These companies invest heavily in research and development to push the boundaries of what is achievable. Technological advancements have only refined the process, with computerized design and simulations ensuring each casting meets exact specifications before physical labor begins. This meticulous attention to detail underscores an authority that only experienced manufacturers can claim, allowing them to deliver castings that stand the test of time.
cast iron casting
Trustworthiness in cast iron casting is cemented on the foundation of rigorous testing and quality assurance. Each product undergoes extensive scrutiny to ensure it meets stringent safety and quality standards. Non-destructive testing methods, such as ultrasonic testing and magnetic particle inspection, provide an added layer of assurance that each casting is flawless and ready to perform. The credibility of a cast iron product is built through these practices, reinforcing confidence in its ability to perform under pressure.
Furthermore, the sustainability of cast iron adds another layer of trustworthiness. As the industry becomes more environmentally conscious, manufacturers have innovated ways to recycle and reuse both the metal and the casting materials. Sand from the molds, for example, is often reclaimed and reused, reducing waste and making the process more sustainable. This environmentally friendly approach not only reduces the carbon footprint but also reinforces the commitment of the industry to sustainable practices.
In a global landscape where precision, reliability, and sustainability are paramount, cast iron casting remains a vital process that industry professionals trust. Its blend of historical expertise and modern technological advancements make it a preferred choice for those seeking quality and longevity. The method’s ability to produce resilient and detailed components continues to secure its position as a go-to solution for heavy-duty industries.
To sum it up, cast iron casting is much more than a manufacturing process; it's a blend of art, science, and a deep-seated trust in a method that has proven itself time and time again. As advances continue to emerge, and as the push for sustainable practices intensifies, cast iron casting will undoubtedly remain integral to industries around the world, reinforcing its status as a cornerstone of industrial manufacturing.