Cast iron panel casting is an ancient yet ever-evolving technique, deeply rooted in industrial history and continuously finding new applications in modern settings. For over two thousand years, the process has been refined to deliver durable and intricate designs, making it invaluable in both architectural and industrial contexts.
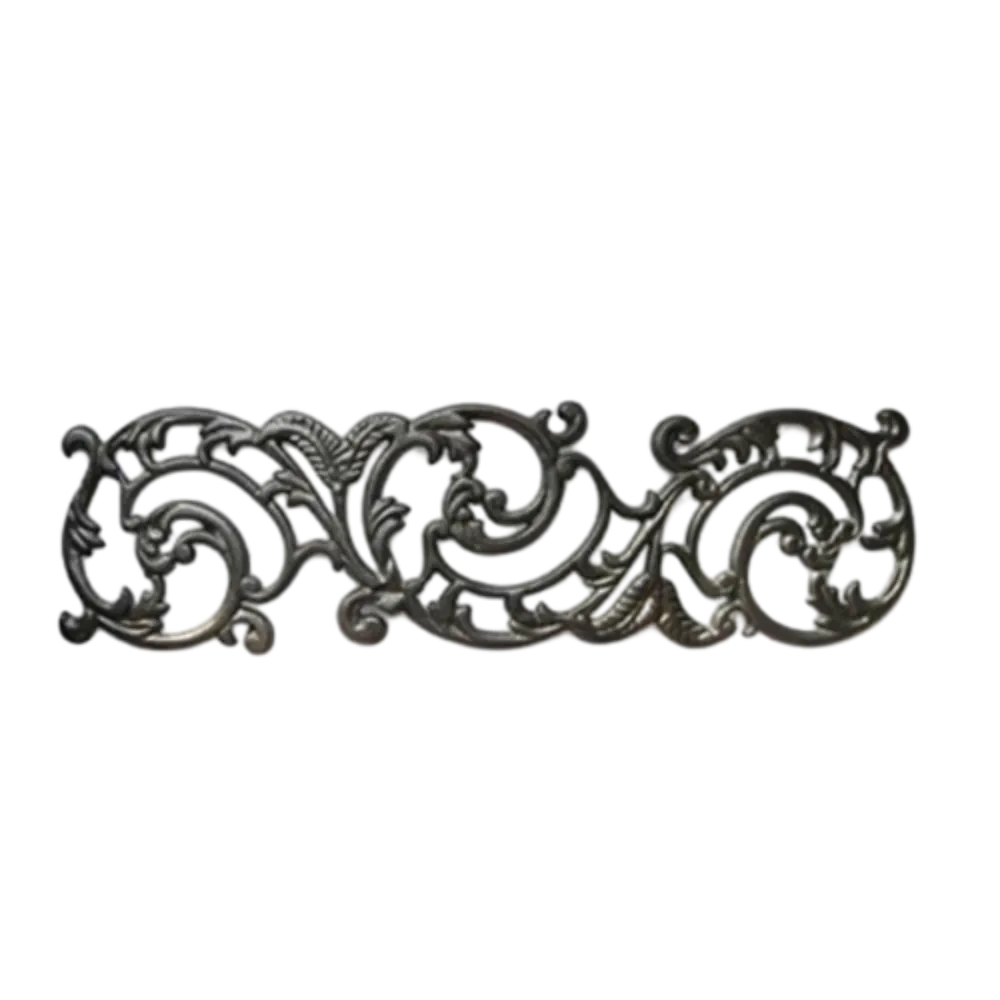
At its core,
the strength of cast iron lies in its composition. Created by melting iron along with carbon and silicon, it is then poured into specialized molds. The resulting cast iron panels are celebrated for their compressive strength, wear resistance, and aesthetic versatility. This combination makes them suitable for everything from industrial machinery to ornate architectural details.
One significant advantage of using cast iron panel casting is its exceptional durability. Resistant to the daily wear and tear that many other materials succumb to, cast iron panels boast a robustness that ensures longevity. This makes them ideal not only for structural purposes but also for elements exposed to harsh outdoor environments. Many urban landscapes utilize cast iron panels in the form of railings, gates, and façade embellishments, showcasing the material's ability to withstand varying weather conditions without compromising visual appeal.

In terms of design flexibility, cast iron panel casting offers unparalleled opportunities for customization. Through the use of sand casting techniques and other molding methods, manufacturers can achieve intricate patterns and precise dimensions. This tailorability is particularly beneficial for architects and designers who seek unique styles while maintaining structural integrity. Historical replicates and restoration projects often rely on cast iron panels to match original designs, preserving the heritage while employing contemporary casting techniques.
cast iron panel casting
Integrating cast iron panel casting into modern projects requires expertise. Professionals in the field must possess advanced knowledge of metallurgical properties to ensure optimal casting outcomes. The alloy composition, cooling rates, and mold designs can significantly impact the final product, and thus, experienced foundry engineers are indispensable. They apply scientific principles to control every aspect of the casting process, ensuring each panel meets specified mechanical properties and aesthetic criteria.
Furthermore, sustainability is a growing consideration in the manufacturing sector, and cast iron panel casting offers eco-friendly benefits. Cast iron is fully recyclable, and the integrity of the metal is maintained through multiple reuses. This reduces the environmental footprint, a critical factor as industries worldwide strive for greener production methods. Leading foundries are adopting closed-loop recycling systems to optimize resource efficiency, aligning with global environmental standards and appealing to eco-conscious consumers.
Safety is another crucial aspect where cast iron excels. Fire resistance is inherent in cast iron panels, making them a preferable choice in construction projects where fire safety codes are stringent. Unlike some modern materials that can degrade or emit harmful fumes under high temperatures, cast iron remains stable, offering peace of mind in public and residential buildings alike.
In conclusion, cast iron panel casting is a testament to the enduring value of traditional materials adapted to contemporary needs. Its combination of durability, design flexibility, expert engineering, sustainability, and safety underpins its continued relevance in a competitive industrial landscape. For those seeking reliable and distinctive solutions in architectural and industrial applications, cast iron panels provide a tried and tested foundation. Embracing this material harnesses centuries of knowledge and adaptation, driving forward an industry committed to quality and resilience.