Cast iron bushings have stood the test of time as indispensable components vital to the performance and longevity of a vast array of machinery. These small, yet mighty, pieces are the unsung heroes facilitating low friction and wear in moving parts, ensuring the seamless operation of devices from industrial machines to vehicles. As someone deeply entrenched in the engineering and manufacturing landscape, the nuances of cast iron bushing selection, usage, and benefits offer a treasure trove of expertise, reliability, and a testament to their unparalleled functionality.

The essence of cast iron bushings lies in their material properties. Known for their robustness and excellent wear resistance, cast iron bushings are an ideal choice for heavy-duty applications where durability is paramount. The natural lubricity of cast iron paired with its ability to withstand extreme temperatures and pressures without deformation makes it an exemplary choice in scenarios where lesser materials would falter.
In an environment where precision machinery operates relentlessly, the metal-on-metal contact can be perilous if not properly managed.
Cast iron bushings act as a sacrificial layer, absorbing the brunt of contact and abrasion. This characteristic extends the lifespan of more critical, costly components, offering a cost-effective solution in demanding industrial settings. Furthermore, the intrinsic strength and wear resistance of cast iron translates into fewer maintenance intervals, contributing to cost-efficiency over the machine’s lifecycle.
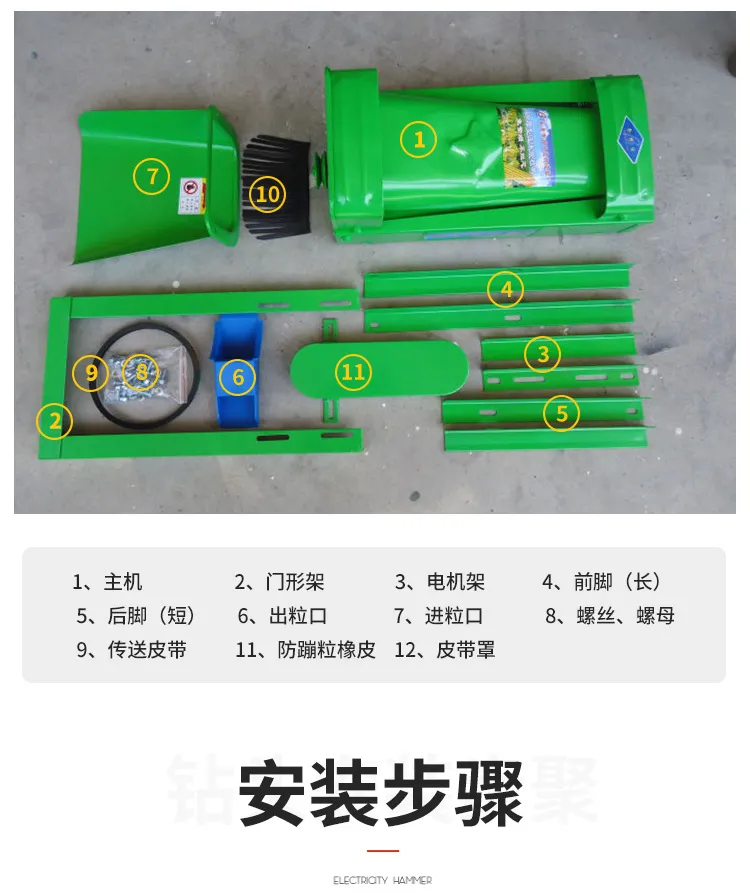
For engineers and maintenance experts, the decision to utilize cast iron bushings is bolstered by their simplicity and reliability. Unlike complex bearing assemblies that require careful and frequent lubrication, cast iron bushings are relatively maintenance-free and can be easily replaced when worn, reducing downtime considerably. This characteristic is crucial in high-output environments where every second of production counts, accentuating their importance in sectors such as manufacturing, automotive, and aerospace.
The trustworthiness of cast iron bushings is rooted in centuries of application and scrutiny. Their efficacy has been recognized and validated through rigorous testing and real-world application, establishing a legacy of performance that engineering professionals can depend on. As technological advancements continue to push the boundaries of what machinery can achieve, the fundamental role of cast iron bushings as reliable facilitators of motion remains unchanged, underpinning modern machines with a layer of historical reliability and engineering efficacy.
cast iron bushings
Authoritativeness in discussing cast iron bushings comes from a wealth of industry knowledge and practical experience. It is not merely the composition of cast iron that makes these bushings exceptional but the application of specific types to various industrial needs. For instance, the integration of graphite into cast iron bushings provides enhanced lubrication properties, optimizing them for conditions where self-lubrication and longevity are critical.
Understanding the environment in which a machine operates allows for the precise tailoring of bushing materials and configurations, ensuring optimal performance. The expertise required to make these determinations cannot be understated. It requires a deep knowledge of material science coupled with an understanding of mechanical demands, ultimately ensuring that machinery operates at peak efficiency, with minimal interruption.
In addition to their technical benefits, the economic aspect of employing cast iron bushings also underscores their importance. The cost-effectiveness of these components is undeniable. They provide a significant return on investment by prolonging the life of costly machinery parts and reducing the frequency and cost of maintenance.
In conclusion, cast iron bushings epitomize a blend of historical reliability and modern engineering necessities. They are foundational to the operation of countless machines and continue to be irreplaceable in their capacity to enhance durability, reduce wear, and provide cost-effective solutions for industrial applications. As such, their presence in any engineer's toolkit is both expected and respected, underscoring their continued relevance in an ever-evolving technological landscape.