Understanding the nuances of welding hinges is essential for professionals and hobbyists striving for excellence in their metalwork projects. Welding hinges, a fundamental component in many structures, are pivotal in securing doors, gates, and panels, providing stability and smooth operation. Whether you're a seasoned welder or stepping into the world of welding, having the right knowledge can significantly enhance the quality of your work.
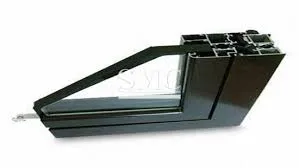
At the core of every welding project involving hinges is the selection of the right type of material. Materials commonly used include steel, stainless steel, and aluminum. Each material brings unique properties that can affect weld strength, corrosion resistance, and aesthetic appeal. For instance, stainless steel hinges are favored in environments prone to moisture due to their anti-rust properties, while aluminum hinges are valued for their lightweight nature.
A crucial factor in successful welding is the choice of welding technique. Techniques such as MIG (Metal Inert Gas) and TIG (Tungsten Inert Gas) welding are popular in hinge welding, each offering distinct advantages. MIG welding is often lauded for its speed and ease of use, making it suitable for beginners or projects where time is of the essence. On the other hand, TIG welding, though more challenging to master, provides high precision and is ideal for projects requiring fine detail and strong weld integrity.
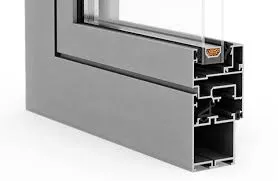
Preparation is another critical aspect when welding hinges. Proper preparation involves cleaning the metal surfaces to be welded, removing any rust, paint, or other contaminants that could weaken the weld. Additionally, securing the hinges in place with clamps ensures they remain in alignment during the welding process, a step that is imperative for maintaining the functionality of the hinges.
welding hings
During the actual welding, maintaining the correct temperature is vital. Too much heat can warp the hinge or weaken the welded joint, whereas insufficient heat may result in an incomplete weld. Investing in a high-quality welder with a reliable temperature control feature can mitigate these risks, ensuring consistent and durable welds.
Safety, often understated, should never be compromised. Wearing appropriate safety gear, including gloves, welding helmets, and protective clothing, is mandatory to protect against burns and eye damage. Furthermore, welding in a well-ventilated area minimizes exposure to potentially harmful fumes, preserving long-term health.
A post-welding inspection is an integral part of the process. Assessing the welds for any signs of cracks or incomplete fusion ensures the longevity and reliability of the hinge. For those seeking a polished finish, grinding the welds and applying a suitable paint or sealant can enhance both the hinge's appearance and durability.
Incorporating these practices not only enhances the quality of welding hinges but also builds a foundation of trust and reliability. By understanding and applying these expert techniques, welders can ensure their projects stand the test of time, offering both functionality and aesthetic appeal. Through dedication, practice, and attention to detail, mastering the art of welding hinges is within reach, paving the way for success in both professional and personal metalworking endeavors.