The production of wrought iron, an essential element in historical architecture and design, is a process steeped in tradition and skill. Unlike its modern counterpart, cast iron, wrought iron is a product of meticulous craftsmanship and precise technique, revered for its remarkable resilience and malleable qualities. The journey of creating wrought iron begins with raw iron ore—usually a combination of iron oxides like hematite (Fe2O3) or magnetite (Fe3O4) extracted from the earth. These ores must undergo multiple stages of refinement to become the wrought iron cherished for both structural and artistic applications.
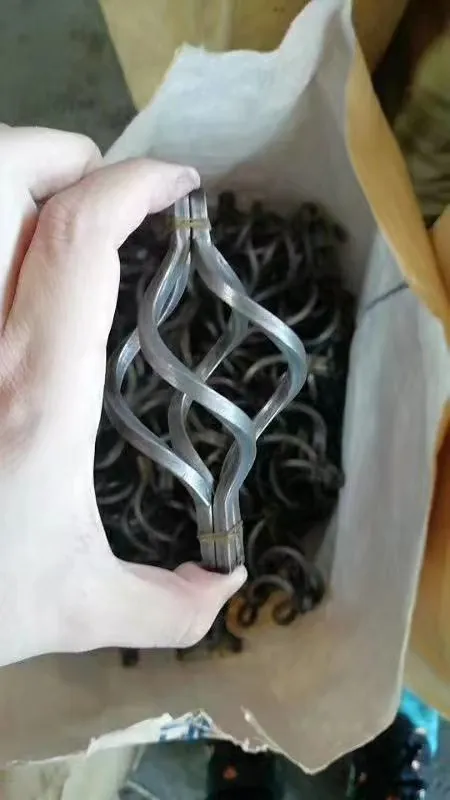
The initial step in manufacturing wrought iron involves smelting the iron ore in a bloomery furnace. Unlike blast furnaces used for producing cast iron, bloomery furnaces operate at lower temperatures, just enough to separate the iron from its ore without melting it completely. This lower-temperature environment is crucial for producing the distinctive fibrous structure of wrought iron, characterized by its layers of iron silicate slag. Throughout this process, the skilled artisan must oversee the combustion of charcoal fuel, ensuring that air flows efficiently through the system to maintain the required heat levels without exceeding them.
As the iron is heated, it forms a mass known as a bloom—a porous conglomerate of iron and slag. Extracting the bloom is a labor-intensive phase that demands both expertise and physical strength. Once the bloom is removed from the furnace, it is meticulously hammered and worked to expel its slag impurities. This hammering process, also known as shingling, requires precision to compact the bloom while maintaining its internal structure. The shingled bloom is then repeatedly heated and worked into a consolidated mass that progressively becomes purer wrought iron.
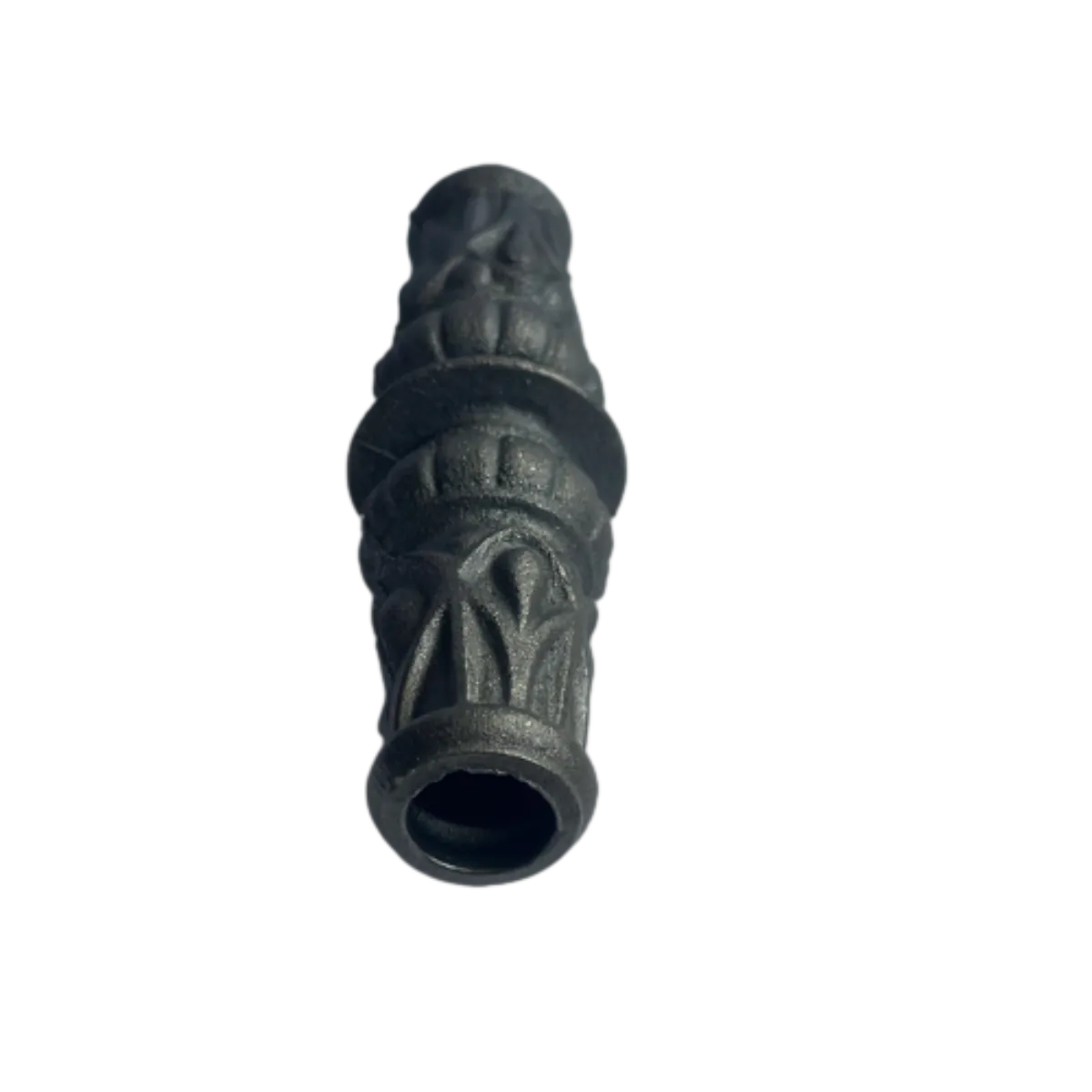
To achieve the unique proprieties of wrought iron—strength, malleability, and resistance to fatigue—continuous refinement is necessary. This involves a sequence of heating and rolling processes where the iron is passed through rolls and worked under various hammers. Each heating session embeds additional layers of slag into the iron matrix, enhancing its fibrous consistency. During this phase, the consistency of the working environment is key. Controlling the temperature and timing allows the craftsman to adjust the properties of the iron to suit different applications, whether they aim to emphasize its ductility for intricate scrollwork or its sturdiness for structural beams.
how is wrought iron produced
Advancements in ironworking technology, such as the introduction of puddling in the 18th century, revolutionized the manufacture of wrought iron, providing opportunities for large-scale production. The puddling process involves the refining of pig iron in a reverberatory furnace, skillfully stirred by a puddler using long rods. This intricate process not only reduces carbon content but also separates and refines impurities, turning the pig iron into pure wrought iron. As the puddler churns the molten mass, carbon levels are meticulously monitored to produce a dependable, uniform material for extensive use.
Wrought iron's distinct characteristics extend beyond its resiliency to corrosion and fatigue; its malleability allows for striking ornamental designs that have stood the test of time. Renowned for its presence in historical landmarks and elegant decorative pieces, wrought iron's allure persists. Despite modern advancements, traditional methods of production remain preserved by artisans and blacksmiths devoted to keeping the legacy alive. Trust in their craftsmanship, coupled with the enduring utility of the product, cements wrought iron's authoritative presence in architecture and product design.
Thus, the manufacture of wrought iron is not merely a process of creating a metal product; it is an art form. Its intricate methods demand not only technical skill but also a comprehensive understanding of the material's properties and behavior. A product of centuries-old expertise, wrought iron embodies a synthesis of tradition, skill, and innovation—qualities that have contributed to its sustained relevance and admiration in both historical and modern contexts.